What are the Latest Manufacturing Processes for Resistor Connections?
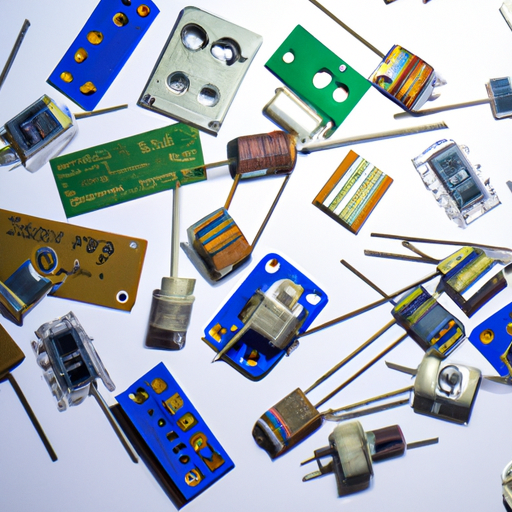
I. Introduction
Resistor connections are fundamental components in electronic circuits, serving to regulate current flow and maintain voltage levels. As the backbone of electronic devices, the reliability and efficiency of these connections are paramount. With the rapid evolution of technology, the manufacturing processes for resistor connections have undergone significant advancements. This blog post explores the latest manufacturing processes, highlighting traditional methods, emerging technologies, advanced materials, automation, environmental considerations, and future trends.
II. Traditional Manufacturing Processes
A. Overview of Conventional Methods
Historically, resistor connections have relied on conventional manufacturing methods such as soldering and wire bonding.
1. **Soldering Techniques**: Soldering is the most common method for connecting resistors to circuit boards. It involves melting a filler metal (solder) to create a conductive joint. While effective, traditional soldering can be time-consuming and requires skilled labor.
2. **Wire Bonding**: This method involves connecting a thin wire from the resistor to the circuit board using ultrasonic energy. Wire bonding is often used in integrated circuits but can be less efficient for larger components.
B. Limitations of Traditional Methods
Despite their widespread use, traditional manufacturing processes have several limitations:
1. **Reliability Issues**: Solder joints can be prone to fatigue and failure over time, especially in high-stress environments. This can lead to circuit malfunctions and increased maintenance costs.
2. **Time Consumption**: The manual nature of soldering and wire bonding can slow down production rates, making it challenging to meet the demands of high-volume manufacturing.
3. **Environmental Concerns**: Traditional soldering often involves lead-based materials, raising environmental and health concerns. The electronics industry is under increasing pressure to adopt greener practices.
III. Emerging Manufacturing Technologies
As the demand for more efficient and reliable resistor connections grows, several emerging technologies are reshaping the manufacturing landscape.
A. Surface Mount Technology (SMT)
1. **Description and Benefits**: SMT involves mounting components directly onto the surface of printed circuit boards (PCBs) rather than inserting them through holes. This method allows for a more compact design and faster assembly.
2. **Impact on Resistor Connection Efficiency**: SMT significantly reduces the time required for assembly and improves the overall reliability of connections. The smaller footprint of surface-mounted resistors also enables more complex circuit designs.
B. Automated Optical Inspection (AOI)
1. **Role in Quality Control**: AOI systems use high-resolution cameras to inspect solder joints and component placements on PCBs. This technology enhances quality control by identifying defects early in the manufacturing process.
2. **Enhancements in Defect Detection**: With advanced algorithms, AOI can detect even the smallest defects that may go unnoticed by the human eye, ensuring higher quality and reliability in resistor connections.
C. Laser Welding
1. **Process Overview**: Laser welding uses focused laser beams to create high-precision connections between resistors and circuit boards. This method is particularly useful for applications requiring minimal thermal impact.
2. **Advantages Over Traditional Soldering**: Laser welding offers several benefits, including reduced thermal stress on components, faster processing times, and the ability to join dissimilar materials without compromising integrity.
D. 3D Printing and Additive Manufacturing
1. **Introduction to 3D Printed Resistors**: 3D printing technology is making its way into resistor manufacturing, allowing for the creation of custom resistors tailored to specific applications.
2. **Customization and Rapid Prototyping Capabilities**: The ability to quickly prototype and produce unique resistor designs can lead to innovations in circuit design and functionality, enabling engineers to experiment with new configurations.
IV. Advanced Materials in Resistor Connections
The materials used in resistor connections are also evolving, leading to improved performance and reliability.
A. Conductive Adhesives
1. **Properties and Applications**: Conductive adhesives are materials that can bond components while providing electrical conductivity. They are increasingly used in place of traditional solder.
2. **Benefits Over Traditional Solder**: Conductive adhesives offer several advantages, including lower processing temperatures, reduced thermal stress, and the ability to bond a wider range of materials.
B. Nanomaterials
1. **Use of Graphene and Carbon Nanotubes**: Nanomaterials, such as graphene and carbon nanotubes, are being explored for their exceptional electrical properties. These materials can enhance the performance of resistors and connections.
2. **Impact on Performance and Miniaturization**: The incorporation of nanomaterials can lead to smaller, more efficient resistor designs, enabling the miniaturization of electronic devices without sacrificing performance.
V. Automation and Industry 4.0
The integration of automation and Industry 4.0 principles is transforming the manufacturing landscape for resistor connections.
A. Role of Robotics in Manufacturing Processes
Robotic systems are increasingly being employed in the assembly and inspection of resistor connections. These systems can perform repetitive tasks with high precision, reducing the risk of human error and increasing production efficiency.
B. Integration of IoT in Resistor Connection Manufacturing
The Internet of Things (IoT) is enabling real-time monitoring and data collection throughout the manufacturing process. This connectivity allows for better tracking of production metrics and can lead to more informed decision-making.
C. Data Analytics for Process Optimization
Data analytics tools are being used to analyze production data, identify bottlenecks, and optimize manufacturing processes. By leveraging data, manufacturers can improve efficiency, reduce waste, and enhance product quality.
VI. Environmental Considerations
As the electronics industry faces increasing scrutiny regarding its environmental impact, manufacturers are adopting more sustainable practices.
A. Eco-Friendly Materials and Processes
The development of eco-friendly materials, such as lead-free solder and biodegradable adhesives, is becoming a priority. These materials help reduce the environmental footprint of resistor connections.
B. Waste Reduction Strategies
Manufacturers are implementing waste reduction strategies, such as recycling and reusing materials, to minimize their impact on the environment. Lean manufacturing principles are also being adopted to streamline processes and reduce waste.
C. Compliance with Global Regulations
With stricter regulations regarding electronic waste and hazardous materials, manufacturers must ensure compliance with global standards. This includes adhering to directives such as RoHS (Restriction of Hazardous Substances) and WEEE (Waste Electrical and Electronic Equipment).
VII. Future Trends in Resistor Connection Manufacturing
The future of resistor connection manufacturing is poised for exciting developments.
A. Predictions for Technological Advancements
As technology continues to evolve, we can expect further advancements in manufacturing processes, including the integration of artificial intelligence (AI) for predictive maintenance and quality control.
B. Potential Impact on the Electronics Industry
These advancements will likely lead to more reliable and efficient electronic devices, driving innovation across various sectors, including consumer electronics, automotive, and healthcare.
C. Importance of Continuous Innovation
To remain competitive, manufacturers must embrace continuous innovation and adapt to changing market demands. This includes investing in research and development to explore new materials and processes.
VIII. Conclusion
In summary, the manufacturing processes for resistor connections are undergoing significant transformation, driven by advancements in technology, materials, and sustainability practices. While traditional methods have served the industry well, emerging technologies such as SMT, laser welding, and 3D printing are paving the way for more efficient and reliable connections. As manufacturers continue to prioritize environmental considerations and embrace automation, the future of resistor connection manufacturing looks promising.
Industry stakeholders must recognize the importance of adopting these new manufacturing processes to stay competitive and meet the evolving demands of the electronics market. By embracing innovation and sustainability, the industry can ensure the continued reliability and efficiency of resistor connections in the ever-evolving landscape of electronic devices.