Common Production Processes for Current Sensing Resistors
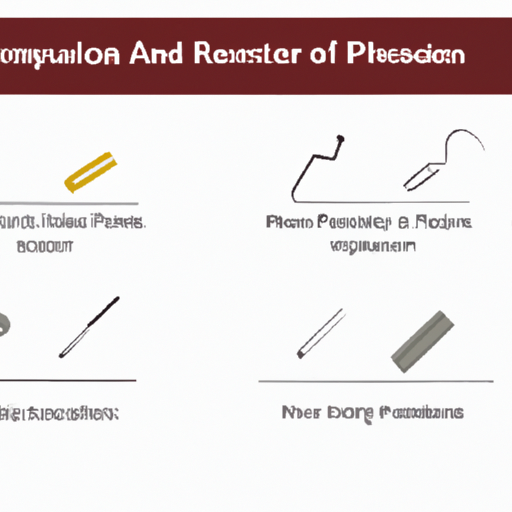
I. Introduction
Current sensing resistors, often referred to as shunt resistors, are critical components in electronic circuits that measure the flow of electric current. By providing a precise resistance value, these resistors allow for accurate current measurement, which is essential in applications ranging from power management systems to automotive electronics. As the demand for efficient and reliable electronic devices continues to grow, understanding the production processes of current sensing resistors becomes increasingly important. This blog post will explore the various types of current sensing resistors, the raw materials used in their production, the common manufacturing processes, innovations in the field, and the challenges faced by manufacturers.
II. Types of Current Sensing Resistors
Current sensing resistors come in several types, each suited for specific applications and performance requirements:
A. Shunt Resistors
Shunt resistors are the most common type of current sensing resistors. They are typically low-resistance components placed in series with the load to measure the current flowing through the circuit. Their low resistance minimizes the impact on the circuit's performance.
B. Wire-Wound Resistors
Wire-wound resistors are made by winding a metal wire around a core. They offer high precision and stability, making them suitable for applications requiring accurate current measurement. However, they can be bulkier than other types.
C. Thin-Film Resistors
Thin-film resistors are created by depositing a thin layer of resistive material onto a substrate. They provide excellent temperature stability and low noise, making them ideal for high-precision applications.
D. Thick-Film Resistors
Thick-film resistors are produced by screen printing a thick layer of resistive paste onto a substrate. They are cost-effective and can be manufactured in various shapes and sizes, making them versatile for different applications.
E. Comparison of Types Based on Application and Performance
When selecting a current sensing resistor, factors such as accuracy, temperature coefficient, size, and cost must be considered. Shunt resistors are often preferred for high-current applications, while thin-film resistors are favored in precision measurement scenarios.
III. Raw Materials Used in Production
The production of current sensing resistors involves various raw materials, each contributing to the resistor's performance and reliability.
A. Conductive Materials
Common conductive materials include copper, nickel, and various alloys. The choice of material affects the resistor's resistance value, temperature coefficient, and overall performance.
B. Substrates
Substrates such as ceramic and polymer are used to support the resistive elements. Ceramic substrates offer excellent thermal stability, while polymer substrates can be lighter and more flexible.
C. Insulating Materials
Insulating materials are essential to prevent unwanted current flow and ensure the resistor operates correctly. These materials must withstand high temperatures and provide electrical isolation.
D. Coatings and Finishes
Protective coatings and finishes are applied to enhance the durability and performance of current sensing resistors. These coatings can provide resistance to environmental factors such as moisture and corrosion.
IV. Common Production Processes
The production of current sensing resistors involves several key processes, each critical to ensuring the final product meets performance specifications.
A. Design and Prototyping
The production process begins with design and prototyping. Engineers use electrical and thermal modeling to simulate the resistor's performance under various conditions. Prototype development allows for testing and refinement before mass production.
B. Material Preparation
Material preparation involves sourcing and quality control of raw materials. Ensuring that materials meet specific standards is crucial for the performance and reliability of the final product. Pre-treatment processes, such as cleaning and surface preparation, are also essential to ensure proper adhesion and performance.
C. Fabrication Techniques
The fabrication of current sensing resistors employs various techniques:
1. Thin-Film Deposition
Thin-film deposition techniques, such as sputtering and evaporation, are used to create thin-film resistors. These methods allow for precise control over the thickness and composition of the resistive layer.
2. Thick-Film Printing
Thick-film resistors are produced using screen printing techniques. The resistive paste is printed onto the substrate, and the ink formulation is critical to achieving the desired resistance value and performance characteristics.
3. Wire-Wound Manufacturing
Wire-wound resistors are manufactured by winding a metal wire around a core. The winding techniques and resistance adjustment processes are crucial to achieving the desired resistance value and ensuring uniformity across production batches.
D. Assembly and Packaging
Once the resistive elements are fabricated, they are assembled and packaged. This process includes mounting the resistors on substrates and applying encapsulation and protective coatings to enhance durability and performance.
E. Testing and Quality Assurance
Testing and quality assurance are critical steps in the production process. Electrical testing measures parameters such as resistance and temperature coefficient, while environmental testing assesses the resistor's performance under various conditions, including humidity and thermal cycling.
V. Innovations in Production Processes
The production of current sensing resistors is continually evolving, with several innovations shaping the industry.
A. Automation and Robotics in Manufacturing
Automation and robotics are increasingly being integrated into the manufacturing process, improving efficiency and precision. Automated systems can handle repetitive tasks, reducing the risk of human error and increasing production speed.
B. Advances in Materials Science
Advancements in materials science have led to the development of new conductive materials and substrates that enhance the performance of current sensing resistors. These innovations can improve temperature stability, reduce noise, and increase overall reliability.
C. Eco-Friendly Production Methods
As sustainability becomes a priority, manufacturers are exploring eco-friendly production methods. This includes using recyclable materials, reducing waste, and implementing energy-efficient processes.
D. Customization and Rapid Prototyping Technologies
The demand for customized solutions is growing, and rapid prototyping technologies allow manufacturers to quickly develop and test new designs. This flexibility enables manufacturers to respond to market needs more effectively.
VI. Challenges in Production
Despite advancements in production processes, manufacturers face several challenges in producing current sensing resistors.
A. Maintaining Precision and Accuracy
Achieving high precision and accuracy in resistor production is critical, especially for applications requiring exact measurements. Variations in material properties or manufacturing processes can lead to inconsistencies.
B. Cost Management
Managing production costs while maintaining quality is a constant challenge. Manufacturers must balance the use of high-quality materials and advanced technologies with the need to keep prices competitive.
C. Supply Chain Issues
Supply chain disruptions can impact the availability of raw materials and components, leading to delays in production. Manufacturers must develop strategies to mitigate these risks and ensure a steady supply of materials.
D. Meeting Regulatory Standards
Compliance with regulatory standards is essential for manufacturers of current sensing resistors. Adhering to industry standards ensures product safety and reliability, but it can also add complexity to the production process.
VII. Conclusion
In summary, current sensing resistors play a vital role in modern electronic applications, and understanding their production processes is essential for manufacturers and engineers alike. From the various types of resistors to the raw materials and fabrication techniques, each aspect contributes to the performance and reliability of these components. Innovations in automation, materials science, and eco-friendly practices are shaping the future of resistor production, while challenges such as precision, cost management, and regulatory compliance remain critical considerations. As technology continues to advance, current sensing resistors will play an increasingly important role in driving innovation and efficiency in electronic systems.
VIII. References
- Academic journals on electrical engineering and materials science.
- Industry reports on current sensing technologies and market trends.
- Manufacturer specifications and guidelines for current sensing resistors.
This comprehensive overview provides insights into the production processes of current sensing resistors, highlighting their significance in the ever-evolving landscape of electronics.