The Production Process of Mainstream Series Capacitors
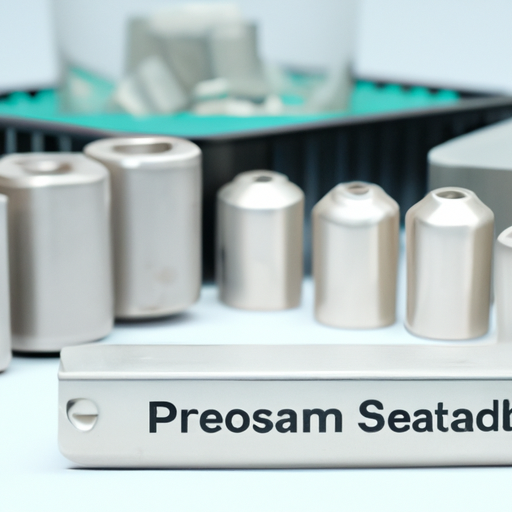
I. Introduction
Capacitors are fundamental components in electronic circuits, serving as energy storage devices that can release energy when needed. They play a crucial role in various applications, from filtering signals in audio equipment to stabilizing voltage in power supplies. Among the different types of capacitors, series capacitors are particularly important in applications where voltage ratings need to be increased or where specific electrical characteristics are required. This article aims to provide a comprehensive overview of the production process of mainstream series capacitors, exploring the types, raw materials, manufacturing steps, and future trends in the industry.
II. Types of Series Capacitors
A. Film Capacitors
Film capacitors are made using thin plastic films as the dielectric material. Common materials include polyester, polypropylene, and polycarbonate. These capacitors are known for their stability, low self-inductance, and excellent frequency characteristics, making them suitable for applications in audio equipment, power electronics, and signal processing.
B. Ceramic Capacitors
Ceramic capacitors utilize ceramic materials as the dielectric. They are categorized into Class 1 (temperature-stable) and Class 2 (high-capacitance) types. Class 1 capacitors are used in precision applications, while Class 2 capacitors are often found in consumer electronics due to their higher capacitance values. Their small size and reliability make them a popular choice in various electronic devices.
C. Electrolytic Capacitors
Electrolytic capacitors are polarized capacitors that use an electrolyte as one of the plates. They are known for their high capacitance values and are commonly used in power supply circuits, audio amplifiers, and energy storage applications. The construction involves a thin oxide layer that acts as the dielectric, typically formed on aluminum or tantalum substrates.
D. Tantalum Capacitors
Tantalum capacitors are known for their high capacitance per volume and stability over a wide temperature range. They are constructed using tantalum metal as the anode and a tantalum oxide layer as the dielectric. These capacitors are often used in applications requiring high reliability, such as in military and aerospace electronics.
III. Raw Materials for Capacitor Production
A. Dielectric Materials
The choice of dielectric material is critical in capacitor production. Common dielectric materials include polyester, polypropylene, ceramic, and tantalum oxide. Each material has unique properties, such as dielectric constant, temperature stability, and voltage rating, which influence the capacitor's performance. Selection criteria often include electrical characteristics, cost, and environmental impact.
B. Conductive Materials
Conductive materials, primarily metals, are essential for capacitor electrodes. Aluminum and tantalum are the most commonly used metals due to their excellent conductivity and compatibility with dielectric materials. Coating materials, such as conductive polymers, may also be used to enhance performance and reliability.
C. Insulating Materials
Insulating materials are crucial for ensuring the safety and efficiency of capacitors. They prevent electrical leakage and protect the internal components from environmental factors. Common insulating materials include epoxy resins and silicone, which also provide mechanical strength and durability.
IV. The Production Process
A. Design and Engineering
The production process begins with design and engineering, where specifications and requirements are established based on the intended application. Engineers create prototypes and conduct testing to ensure that the design meets performance standards. This phase is critical for identifying potential issues early in the production process.
B. Material Preparation
Once the design is finalized, the next step involves sourcing raw materials. Quality control measures are implemented to ensure that all materials meet the required standards. Pre-processing of materials, such as cutting films or preparing metal substrates, is also performed to facilitate the subsequent manufacturing steps.
C. Dielectric Layer Formation
The formation of the dielectric layer varies depending on the type of capacitor. For film capacitors, the dielectric film is produced through extrusion or casting processes. In ceramic capacitors, the dielectric is formed by sintering ceramic powders at high temperatures. For electrolytic and tantalum capacitors, the dielectric layer is created through anodization, where an oxide layer is formed on the metal substrate.
D. Electrode Fabrication
Electrode fabrication involves depositing conductive materials onto the dielectric layer. Various methods, such as sputtering, chemical vapor deposition, or screen printing, are used to create the electrodes. The surface area of the electrodes is crucial, as a larger surface area increases the capacitance and overall performance of the capacitor.
E. Assembly
The assembly process involves stacking and aligning the dielectric and electrode layers. This step is critical for ensuring that the capacitor functions correctly. After stacking, the components are encapsulated and sealed to protect them from environmental factors and mechanical stress. Encapsulation materials are chosen for their insulating properties and durability.
F. Testing and Quality Assurance
Once assembled, capacitors undergo rigorous testing to ensure they meet electrical and environmental standards. Electrical testing includes measuring capacitance, equivalent series resistance (ESR), and leakage current. Environmental testing assesses the capacitor's performance under various conditions, such as temperature and humidity. Reliability testing simulates long-term usage to identify potential failure modes.
V. Environmental and Safety Considerations
The production of capacitors involves various environmental and safety considerations. Waste management practices are essential to minimize the environmental impact of manufacturing processes. Compliance with regulations, such as the Restriction of Hazardous Substances (RoHS) and Registration, Evaluation, Authorisation and Restriction of Chemicals (REACH), ensures that harmful substances are not used in production. Safety measures, including proper handling of materials and equipment, are implemented to protect workers and the environment.
VI. Innovations and Future Trends
The capacitor industry is witnessing significant innovations driven by advances in materials science. Researchers are exploring new dielectric materials that offer higher capacitance and improved performance. Miniaturization is another trend, with manufacturers developing smaller capacitors that maintain high performance, catering to the demand for compact electronic devices. Additionally, sustainable practices are gaining traction, with companies focusing on reducing waste and using eco-friendly materials in production.
VII. Conclusion
The production process of mainstream series capacitors is a complex and multifaceted endeavor that involves careful consideration of materials, design, and manufacturing techniques. As technology continues to evolve, the importance of quality and innovation in capacitor manufacturing cannot be overstated. The future outlook for series capacitors is promising, with ongoing advancements in materials and production processes paving the way for more efficient and reliable electronic components.
VIII. References
1. Academic journals on capacitor technology and materials science.
2. Industry reports on trends and innovations in capacitor manufacturing.
3. Manufacturer guidelines and specifications for various types of capacitors.
---
This blog post provides a detailed overview of the production process of mainstream series capacitors, highlighting the importance of each step and the materials involved. By understanding this process, readers can appreciate the complexity and significance of capacitors in modern electronics.