The Production Process of Mainstream Low-Voltage Capacitors
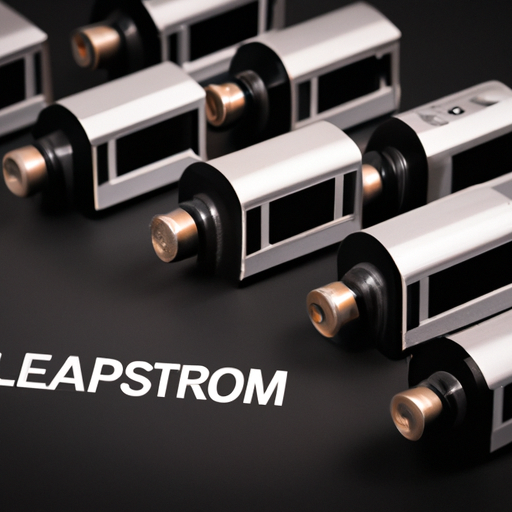
I. Introduction
Low-voltage capacitors are essential components in a wide array of electronic devices, from smartphones and computers to household appliances and industrial machinery. These capacitors store and release electrical energy, helping to stabilize voltage and power flow within circuits. As technology advances, the demand for efficient, reliable, and compact capacitors has surged, leading to innovations in their production processes. This blog post will explore the various types of low-voltage capacitors, the raw materials used in their manufacture, the detailed production process, environmental considerations, and recent innovations in the field.
II. Types of Low-Voltage Capacitors
Low-voltage capacitors come in several types, each with unique characteristics and applications:
A. Ceramic Capacitors
Ceramic capacitors are widely used due to their small size, low cost, and stability. They are made from ceramic materials that act as the dielectric. These capacitors are ideal for high-frequency applications and are commonly found in RF circuits and decoupling applications.
B. Electrolytic Capacitors
Electrolytic capacitors are polarized capacitors that offer high capacitance values in a relatively small package. They are typically used in power supply circuits and audio applications. Their construction involves a liquid or gel electrolyte, which allows for a larger surface area and higher capacitance.
C. Film Capacitors
Film capacitors use a thin plastic film as the dielectric material. They are known for their stability, low loss, and excellent performance in high-frequency applications. Film capacitors are often used in audio equipment, power electronics, and timing circuits.
D. Tantalum Capacitors
Tantalum capacitors are known for their high capacitance-to-volume ratio and reliability. They are often used in applications where space is limited, such as in mobile devices and medical equipment. Their construction involves tantalum metal, which provides excellent performance characteristics.
E. Comparison of Different Types
Each type of capacitor has its advantages and disadvantages, making them suitable for specific applications. For instance, while ceramic capacitors are great for high-frequency applications, electrolytic capacitors excel in power supply circuits due to their high capacitance. Understanding these differences is crucial for selecting the right capacitor for a given application.
III. Raw Materials
The production of low-voltage capacitors relies on various raw materials, each contributing to the capacitor's performance and reliability.
A. Overview of Materials Used in Low-Voltage Capacitors
1. **Dielectric Materials**: The dielectric material is crucial for a capacitor's function. Common dielectric materials include ceramic, plastic films, and electrolytic solutions. The choice of dielectric affects the capacitor's capacitance, voltage rating, and temperature stability.
2. **Conductive Materials**: Conductive materials, such as aluminum, tantalum, and copper, are used for the electrodes. The quality and purity of these materials directly impact the capacitor's performance and longevity.
3. **Packaging Materials**: The encapsulation and packaging materials protect the capacitor from environmental factors and mechanical stress. Common materials include epoxy resins and plastic housings.
B. Sourcing and Quality Control of Raw Materials
Sourcing high-quality raw materials is critical for ensuring the reliability of low-voltage capacitors. Manufacturers often establish strict quality control measures, including supplier audits and material testing, to ensure that all materials meet industry standards.
IV. Production Process
The production of low-voltage capacitors involves several key steps, from design and engineering to manufacturing and quality assurance.
A. Design and Engineering
1. **Specifications and Requirements**: The production process begins with defining the specifications and requirements for the capacitor, including capacitance, voltage rating, and size.
2. **Prototyping and Testing**: Engineers create prototypes to test the design's performance. This phase may involve multiple iterations to refine the design before mass production.
B. Manufacturing Steps
1. **Dielectric Layer Preparation**
- **Material Selection**: The first step in manufacturing is selecting the appropriate dielectric material based on the capacitor's intended application.
- **Layer Formation Techniques**: Techniques such as tape casting, screen printing, or vacuum deposition are used to create the dielectric layer.
2. **Electrode Fabrication**
- **Material Deposition Methods**: Electrode materials are deposited onto the dielectric layer using methods like sputtering or chemical vapor deposition.
- **Electrode Patterning**: The electrodes are patterned using photolithography or laser cutting to achieve the desired shape and size.
3. **Assembly**
- **Layer Stacking**: The dielectric and electrode layers are stacked together to form the capacitor structure.
- **Connection of Electrodes**: The electrodes are connected to external leads, ensuring proper electrical connectivity.
4. **Encapsulation**
- **Protective Coatings**: A protective coating is applied to shield the capacitor from environmental factors such as moisture and dust.
- **Packaging for Durability**: The final product is packaged in durable materials to ensure it can withstand handling and transportation.
C. Quality Assurance
1. **Testing Methods**: Capacitors undergo rigorous testing to ensure they meet performance specifications. Tests may include capacitance measurement, leakage current testing, and temperature cycling.
2. **Compliance with Industry Standards**: Manufacturers must comply with industry standards, such as those set by the International Electrotechnical Commission (IEC) and the American National Standards Institute (ANSI), to ensure product reliability and safety.
V. Environmental Considerations
As the electronics industry grows, so does the need for sustainable practices in capacitor production.
A. Sustainable Practices in Capacitor Production
Manufacturers are increasingly adopting sustainable practices, such as using eco-friendly materials and reducing energy consumption during production. This not only helps the environment but also meets consumer demand for greener products.
B. Recycling and Disposal of Capacitors
Proper recycling and disposal of capacitors are essential to minimize environmental impact. Many manufacturers are developing programs to recycle old capacitors and recover valuable materials, reducing waste and promoting sustainability.
C. Regulatory Compliance and Environmental Impact
Compliance with environmental regulations is crucial for manufacturers. This includes adhering to laws regarding hazardous materials and waste management, ensuring that production processes do not harm the environment.
VI. Innovations in Low-Voltage Capacitor Production
The capacitor industry is witnessing significant innovations that enhance performance and efficiency.
A. Advances in Materials Science
Research in materials science is leading to the development of new dielectric and conductive materials that improve capacitor performance, such as higher capacitance values and better thermal stability.
B. Automation and Smart Manufacturing
Automation in the production process is increasing efficiency and reducing costs. Smart manufacturing technologies, such as IoT and AI, are being integrated into production lines to monitor quality and optimize processes in real-time.
C. Future Trends in Capacitor Technology
The future of capacitor technology may include the development of supercapacitors, which offer higher energy density and faster charging times, making them suitable for applications in electric vehicles and renewable energy systems.
VII. Conclusion
The production process of mainstream low-voltage capacitors is a complex and multifaceted endeavor that involves careful consideration of materials, design, and manufacturing techniques. As technology continues to evolve, the significance of low-voltage capacitors in modern electronics cannot be overstated. They play a crucial role in ensuring the reliability and efficiency of electronic devices. Looking ahead, the capacitor industry is poised for exciting advancements that will further enhance performance and sustainability, meeting the demands of an increasingly electronic world.
VIII. References
1. Academic journals on capacitor technology and materials science.
2. Industry reports from leading capacitor manufacturers.
3. Manufacturer guidelines and specifications for low-voltage capacitors.
This comprehensive overview of the production process of low-voltage capacitors highlights the intricate steps involved and the importance of these components in modern electronics. As the industry continues to innovate, the future of capacitors looks promising, paving the way for more efficient and sustainable electronic devices.