What are the Product Standards for DC Resistors?
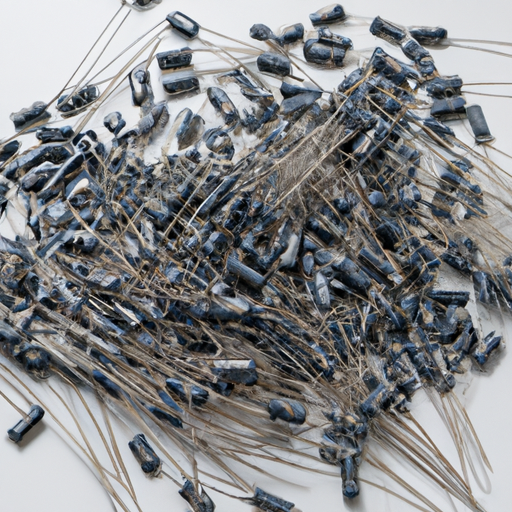
I. Introduction
A. Definition of DC Resistors
DC resistors are passive electronic components that resist the flow of direct current (DC) in a circuit. They are fundamental to electronic design, serving various functions such as limiting current, dividing voltages, and dissipating energy. Resistors are characterized by their resistance value, which is measured in ohms (Ω), and they come in various forms, including fixed, variable, and specialty resistors.
B. Importance of Product Standards
Product standards for DC resistors are crucial for ensuring that these components perform reliably and safely in electronic applications. Standards provide guidelines for manufacturing, testing, and quality assurance, which help maintain consistency across products and manufacturers. This is particularly important in industries where precision and safety are paramount, such as automotive, telecommunications, and medical devices.
C. Overview of the Document Structure
This blog post will explore the various product standards for DC resistors, their significance, key standards, testing processes, and future trends in standardization. By understanding these aspects, manufacturers and engineers can ensure that their products meet the necessary requirements for quality and safety.
II. Understanding DC Resistors
A. Basic Principles of Resistors
1. Ohm's Law
Ohm's Law is the fundamental principle governing the behavior of resistors. It states that the current (I) flowing through a conductor between two points is directly proportional to the voltage (V) across the two points and inversely proportional to the resistance (R) of the conductor. This relationship is expressed mathematically as:
\[ V = I \times R \]
This equation is essential for designing circuits and selecting appropriate resistors for specific applications.
2. Types of Resistors
There are several types of resistors, including:
Fixed Resistors: These have a constant resistance value and are the most common type used in circuits.
Variable Resistors: Also known as potentiometers or rheostats, these allow the resistance value to be adjusted.
Specialty Resistors: These include thermistors, photoresistors, and others designed for specific applications.
B. Applications of DC Resistors
1. Electronic Circuits
DC resistors are widely used in electronic circuits for various purposes, such as current limiting, voltage division, and signal conditioning. They play a critical role in ensuring that circuits operate within their specified parameters.
2. Power Distribution
In power distribution systems, resistors are used for load balancing and to manage power flow. They help prevent overloads and ensure that electrical systems operate efficiently.
3. Signal Processing
In signal processing applications, resistors are used in filters, amplifiers, and other circuits to manipulate signal characteristics. They are essential for achieving desired frequency responses and signal integrity.
III. Importance of Product Standards
A. Ensuring Quality and Reliability
Product standards help ensure that DC resistors meet specific quality and reliability criteria. By adhering to established standards, manufacturers can produce components that perform consistently and meet customer expectations.
B. Safety Considerations
Safety is a critical concern in electronic design. Standards help mitigate risks associated with electrical components, such as overheating, short circuits, and failures. Compliance with safety standards protects both users and equipment.
C. Facilitating Interoperability
In a global market, interoperability between components from different manufacturers is essential. Standards provide a common framework that ensures compatibility, allowing engineers to mix and match components without concerns about performance issues.
D. Regulatory Compliance
Many industries are subject to regulatory requirements that mandate compliance with specific standards. Adhering to these standards helps manufacturers avoid legal issues and ensures that their products can be marketed in various regions.
IV. Key Product Standards for DC Resistors
A. International Standards
1. IEC (International Electrotechnical Commission)
The IEC develops international standards for electrical and electronic devices, including resistors. Their standards cover various aspects, such as performance, safety, and testing methods.
2. ISO (International Organization for Standardization)
ISO standards focus on quality management and assurance. While not specific to resistors, ISO standards can influence manufacturing processes and quality control measures in resistor production.
B. National Standards
1. ANSI (American National Standards Institute)
ANSI oversees the development of standards in the United States, including those related to electrical components. ANSI standards ensure that products meet specific performance and safety criteria.
2. JIS (Japanese Industrial Standards)
JIS standards govern the quality and performance of electrical components in Japan. Compliance with JIS standards is essential for manufacturers looking to enter the Japanese market.
C. Industry-Specific Standards
1. Automotive Standards (e.g., AEC-Q200)
The AEC-Q200 standard outlines reliability requirements for passive components used in automotive applications. Compliance with this standard is crucial for manufacturers supplying components to the automotive industry.
2. Telecommunications Standards
Telecommunications standards ensure that components used in communication systems meet specific performance and reliability criteria. These standards are vital for maintaining the integrity of communication networks.
V. Testing and Certification Processes
A. Overview of Testing Methods
1. Resistance Measurement
Resistance measurement is a fundamental test for DC resistors. It ensures that the resistor's value falls within the specified tolerance range.
2. Temperature Coefficient Testing
The temperature coefficient of resistance (TCR) indicates how much a resistor's value changes with temperature. Testing for TCR is essential for applications where temperature variations are expected.
3. Power Rating Tests
Power rating tests determine the maximum power a resistor can handle without failure. This is critical for ensuring that resistors can operate safely within their specified limits.
B. Certification Bodies
1. UL (Underwriters Laboratories)
UL is a global safety certification organization that tests and certifies electrical components, including resistors. Their certification ensures that products meet safety and performance standards.
2. CSA (Canadian Standards Association)
CSA provides certification for electrical components in Canada. Compliance with CSA standards is essential for manufacturers looking to sell products in the Canadian market.
3. TUV (Technischer Überwachungsverein)
TUV is a German certification body that tests and certifies electrical components for safety and performance. Their certification is recognized internationally.
VI. Common Specifications and Parameters
A. Resistance Value Tolerance
Tolerance indicates the allowable deviation from the nominal resistance value. Common tolerances include ±1%, ±5%, and ±10%, with tighter tolerances required for precision applications.
B. Power Rating
The power rating specifies the maximum power a resistor can dissipate without overheating. This is typically expressed in watts (W) and is critical for ensuring safe operation.
C. Temperature Coefficient
The temperature coefficient indicates how much the resistance value changes with temperature. A lower temperature coefficient is desirable for applications requiring stability over varying temperatures.
D. Voltage Rating
The voltage rating specifies the maximum voltage that can be applied across a resistor without risk of breakdown. This is important for ensuring safe operation in high-voltage applications.
E. Noise Characteristics
Noise characteristics refer to the amount of electrical noise generated by a resistor. Low-noise resistors are essential in sensitive applications, such as audio and precision measurement systems.
VII. Challenges in Standardization
A. Variability in Manufacturing Processes
Manufacturing processes can vary significantly between different manufacturers, leading to inconsistencies in product performance. Standardization helps mitigate these issues, but challenges remain.
B. Evolving Technology and Applications
As technology advances, new applications for resistors emerge, necessitating updates to existing standards. Keeping standards current with technological advancements is a continuous challenge.
C. Global Market Considerations
In a global market, manufacturers must navigate different standards and regulations across regions. This complexity can hinder the standardization process and create barriers to entry for new products.
VIII. Future Trends in DC Resistor Standards
A. Advances in Material Science
Innovations in material science are leading to the development of new resistor types with improved performance characteristics. Standards will need to evolve to accommodate these advancements.
B. Integration with Smart Technologies
As electronic devices become smarter, resistors will play a role in enabling advanced functionalities. Standards will need to address the unique requirements of smart technologies.
C. Sustainability and Environmental Standards
With increasing focus on sustainability, standards will likely incorporate environmental considerations, such as the use of eco-friendly materials and energy-efficient manufacturing processes.
IX. Conclusion
A. Recap of the Importance of Standards
Product standards for DC resistors are essential for ensuring quality, safety, and interoperability in electronic applications. They provide a framework for manufacturers to produce reliable components that meet industry requirements.
B. The Role of Standards in Innovation and Safety
Standards not only facilitate innovation by providing guidelines for new technologies but also ensure that safety considerations are prioritized in product design and manufacturing.
C. Call to Action for Manufacturers and Engineers
Manufacturers and engineers must stay informed about current standards and actively participate in the standardization process. By doing so, they can contribute to the development of high-quality, safe, and reliable DC resistors that meet the needs of a rapidly evolving market.
X. References
A. List of Standards Organizations
- International Electrotechnical Commission (IEC)
- International Organization for Standardization (ISO)
- American National Standards Institute (ANSI)
- Japanese Industrial Standards (JIS)
B. Relevant Literature and Research Papers
- Research papers on resistor technology and applications
- Industry reports on electronic components and standards
C. Industry Reports and Guidelines
- Guidelines from certification bodies such as UL, CSA, and TUV
- Industry standards documents related to DC resistors and their applications
---
This blog post provides a comprehensive overview of the product standards for DC resistors, highlighting their significance, key standards, testing processes, and future trends. By understanding these aspects, stakeholders can ensure that their products meet the necessary requirements for quality and safety in the ever-evolving electronic landscape.